Most people know that a concrete batching plant contains a series of components that work in synergy to produce useable concrete. Most also know that the raw materials required to manufacture high-grade concrete include sand, cement powder, slag, fly ash, silica fume, uncontaminated water, additive agents, air, and a selection of aggregates, such as river stone, pebbles, and gravel. Aggregate batchers, cement silos, dust collectors, heaters, mixers, digital control units, and conveyors are some of the main batching plant components and the information is common knowledge to most in the construction industry.
Mixing Components
The mixer is without a doubt one of the most essential components in a concrete plant. A range of different mixer configurations exists in the market, including pan, twin shaft, planetary, single shaft, and tilt drum. For those seeking generic concrete mixes with uniform consistency, a twin-shaft design is an ideal choice due to its high-power motor. Refer to AIMIX GROUP website to learn more detailed info. Meanwhile, for those that want to produce modified concrete formulas in large batches, a tilt drum mixer design may be a better choice. In North America, twin shaft mixers are the most popular, whereas, in Asian and European continents, tilt drum mixers are more commonplace. The other types of mixers aforementioned are generally reserved for precast applications.
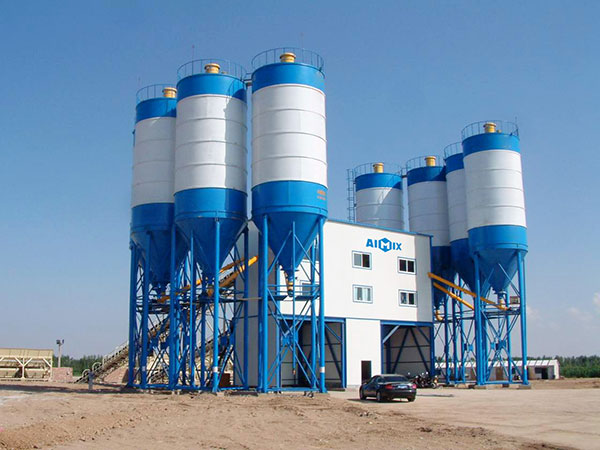
Plant Types
Concrete manufacturing plants tend to be grouped into various core types, such as stationery, mobile, wet mix, and dry mix. Mobile, aka portable, concrete batch plants currently offer the best value for money for temporary construction projects as the average Indonesia batching plant price for mobile designs is competitive. Meanwhile, stationary concrete plants present a great investment option for those seeking mass-scale high-grade concrete production from a single location for an extended duration. Such plants are ideal for port, bridge, skyscraper, dam, and tunnel construction projects. Highlightable features of stationary concrete plants include excellent energy efficiency and proven stability under high intensity.
Notable Applications
Batching plants have an extensive range of notable applications including ready mix mass-production and civil infrastructure projects. The reality is that the market for ready mix concrete is huge and manufacturers stand to make a great return on their investment. Prominent voices forecast the market to exceed US$620 billion in just six years’ time. Ready-mix concrete manufacturing plants must typically adhere to higher standards of reliability, safety, and environmental protections as they tend to be located near or within populous cities.
Concrete Plants And Environmental Pollution
There is no getting away from the fact that the manufacturing of concrete has a negative impact on the environment. This is because the process produces air pollution and uses huge volumes of clean water. The polluting nature of concrete plants means they are not often approved for assembly near residential areas. Fortunately, modern batch plants are now fitted with highly effective dust collection devices as standard and are incredibly more energy efficient, which reduces their carbon footprint. Some newer plants also come equipped with sophisticated water recycling features that limit the impact such plants have on local water supplies and natural bodies of water. If you are looking to invest in one of the latest designs, be sure to check out the competitive Indonesia batching plant harga from the country’s top-rated suppliers.